ERP Master Data: Risks for Mid-Sized Businesses
Medium sized businesses run a larger risk with incorrect ERP master data design than either large or small businesses. Medium sized businesses are large enough and confident enough to think they know what the future holds, but small enough and nimble enough to be able to change directions if their predictions are wrong. These are good business behaviors, but they can play havoc with ERP master data, because medium sized businesses are large enough to make fundamental changes to master data painful.
Let’s look at things that tend to happen when dealing with ERP master data. For example, your a mid-sized manufacturer implementing ERP. Your company manufactures ceramic floor tiles, and they are packaged seven to a carton. Seven tiles was chosen because the weight was in the tolerance that people felt comfortable handling, and the same box could be used for seven floor tiles, seventy-two shower tiles, or twenty-eight decorative tiles for a backsplash.
A Master Data Nightmare
When it came time to assign ERP material numbers, marketing was adamant – 100% sure, no reservations, absolutely correct – that they would always sell tiles in full cartons. The implementation team took this commitment to heart, and made several logical decisions. First they assigned a material number to a carton of tiles, and made it a salable product. Then, without much debate, they made the base unit of measure one carton. Orders were taken in cartons, bill of ladings were referenced in cartons, and revenue was generated in cartons.
All cruised along well for a bit, and then sales growth stalled. Consultants were brought in to study the market and the first conclusion they reached was that your company was losing sales because you didn’t sell individual tiles. Reacting aggressively, your marketing president put out an email that very day, that said, effective immediately, individual tiles were available for sale.
Intuitively, this seems like a reasonable business request.
Realistically, this is an ERP master data nightmare. The only way to process an order for individual tiles is to enter it as a fraction of a container. Fractional orders leave inventory residues, do not calculate pricing or costing logically, and may or may not even be set up for allowing fractions to be taken. So the decision is rapidly made to crash on the thousands of materials needed to sell all tiles as individual, one-at-a-time items, except none of the new material numbers are reflected on the hundreds of thousands of dollars worth of merchandising literature out in the field, so people continue to order fractions of cartons.
All of this could have been avoided by establishing a single tile as the base unit of measure from the start, and establishing a carton as a logical aggregate of that base. Instead, even though everybody made the best possible decisions they could with the information they had, nothing works particularly well. To add to the frustration, sales remain flat; selling individual tiles creates lots of orders but almost no additional revenue.
Think through ERP master data decisions carefully.
Free white paper
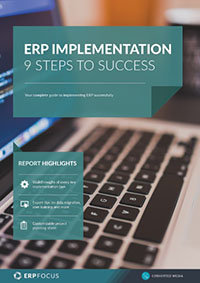
ERP Implementation: 9 steps to success
The 9 proven steps you should follow when implementing ERP
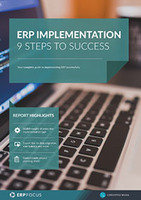
Featured white papers
-
ERP Software Pricing Guide
Get the latest pricing information on over 80 popular ERP systems, and learn how to budget for your ERP project in our free guide
Download -
60-Step ERP Selection Checklist
Get the comprehensive checklist for your ERP selection project
Download -
ERP Implementation: 9 steps to success
The 9 proven steps you should follow when implementing ERP
Download
Related articles
-
ERP migration steps (your ERP migration checklist)
How to construct the smoothest ERP migration plan possible
-
CMMC Compliance: What Aerospace and Defense Manufacturers Need to Know
Key insights on CMMC compliance, deadlines, and securing DoD contracts with CMMC 2.0 certificatio...
-
4 practical examples of the power of real-time ERP data
Discover the potential of real-time data with these practical examples from a range of industries.