ERP and product traceability
We are surrounded by product traceability, some of it apparent and some less so. We see it every time we fill out a warranty card for our new PC, camera or kitchen gadget and it has a box for the item's serial number. Amongst other things, that serial number allows the manufacturer to quickly identify when the item was delivered or sold; ensuring that any applicable warranties are correctly applied only when they remain valid.
But there is more to traceability than warranty management because product safety can also be a massive issue, and that usually requires tracking by lot or batch number also. Just about every item of processed food that we buy will have a lot, or batch, number, and just about everything on that airliner you are about to board has a lot number, serial number, or both.
Most of us will be aware of product recalls being carried out by everyone from automobile manufacturers to supermarkets, but not all of us will have considered what part lot or serial number traceability has to play in the process and, perhaps, even fewer realize that the need to track product via a hard-copy paper chase was, for companies with good ERP systems, consigned to history many years ago.
Nowadays, when a problem with a product is reported, a properly implemented ERP system can, within minutes, report what we can call bidirectional traceability. Take a store-bought pizza as an example. First of all, the individual store where the problem is reported will pull all remaining stock from their shelves. Then the system will tell them if there is any more of that product in their warehouse or at their central distribution point.
Passing word all the way back along the supply chain to the manufacturer allows everyone to see if they have any suspect product in stock, when the manufacturer is told the lot number, the first thing that they can do is to identify any other customers that received part of that suspect batch. But the system can do more than that.
Continuing with the pizza as an example; from its lot number the manufacturer can identify the lot numbers of all the ingredients that went into it and can again ask, “Where are the rest of those batches, and where did they go?” (this is the bidirectionality that was mentioned earlier). And if any of the ingredients are suspect, the same questions can be asked by the suppliers of those items.
All of these questions can be asked and answered in less time than it would take to pull hard-copy documents from an archive, and a fraction of the time it would take to read and analyze them. And although this example has used a pizza as an example, the same requirements and opportunities are found in a range of industries from pharmaceuticals to aerospace.
How does it work?
The lot tracking and serial number tracking begin when components, materials, or ingredients are first received into the factory from suppliers. Most will come with lot numbers or serial numbers already allocated but on occasion will have to be generated by the receiving company. At the point of entering the receipt into the system, a batch record will be created and this will typically hold information such as the following against every lot number or serial number:
- source (usually the purchase order number)
- supplier reference (typically the supplier's delivery note number)
- any relevant expiry, use by, or sell-by dates
- incoming inspection results
- and batch quantity
When materials are required in the production area, ERP can generate a 'pick list' that directs picking staff to the oldest batches to ensure that those are used first, and these items are then issued to the job being made, whether sub-assembly (pizza base) or end product. When these items are received to stock, a batch record very similar to the purchasing batch record is also created.
Eventually, a finished batch of, e.g. pizza bases, is completed and given its own lot number, and at this point, the system knows which batches of bases were used, which batches of flour, etc were used in those bases along with the origin of every ingredient considered worthy of tracking.
What needs to be considered?
The process is actually as easy as it sounds, although some companies have to do a little extra thinking to get it all to work. One consideration, when holding materials in bulk storage such as a silo or tank, is that it can be impractical or even impossible to fully empty that unit before accepting a new receipt. So although theoretically 'batch 2' was used, there could well have been some batch 1 and batch 3 in there as well.
Companies usually get around this by ´bracketing' the theoretical batch and experience will tell them how many batches before and after batch 2 to take into consideration.
A second point, closely allied to this but also occurring when materials are manually selected, is what to do when more than one batch is used (although this is, in fact, forbidden in some industries, such as pharmaceuticals). As with the first consideration, any batch that could have been involved must be assumed to have been involved.
And lastly, there must be discipline in place, particularly when backflushing materials, to ensure that the batches pulled for use are those that were called for on the picklist, and there must also be a company culture that allows the shop floor, if it was necessary to use different batches, to report what they actually did use; without fear of reprisal.
Hopefully, all of this functionality will rarely be needed but, even if it is never used, it can be a very impressive thing to demonstrate to both existing and prospective customers.
Free white paper
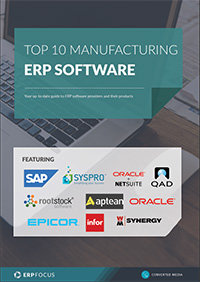
Top 10 Manufacturing ERP Software Comparison
Compare the best manufacturing ERP systems
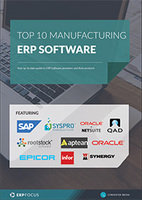
Featured white papers
-
ERP Software Pricing Guide
Get the latest pricing information on over 80 popular ERP systems, and learn how to budget for your ERP project in our free guide
Download -
60-Step ERP Selection Checklist
Get the comprehensive checklist for your ERP selection project
Download -
ERP Implementation: 9 steps to success
The 9 proven steps you should follow when implementing ERP
Download
Related articles
-
ERP & Logistics: Optimizing the Supply Chain
Read about the steps you can take to optimize your supply chain through ERP software logistics ma...
-
CMMC Compliance: What Aerospace and Defense Manufacturers Need to Know
Key insights on CMMC compliance, deadlines, and securing DoD contracts with CMMC 2.0 certificatio...
-
ERP Automation Tips for Your Supply Chain
Learn about the stages in your company’s supply chain which can be optimized through ERP automation.